Understanding How Directional Drilling Is Used With Wells
- By Admin
- •
- 18 May, 2018
- •
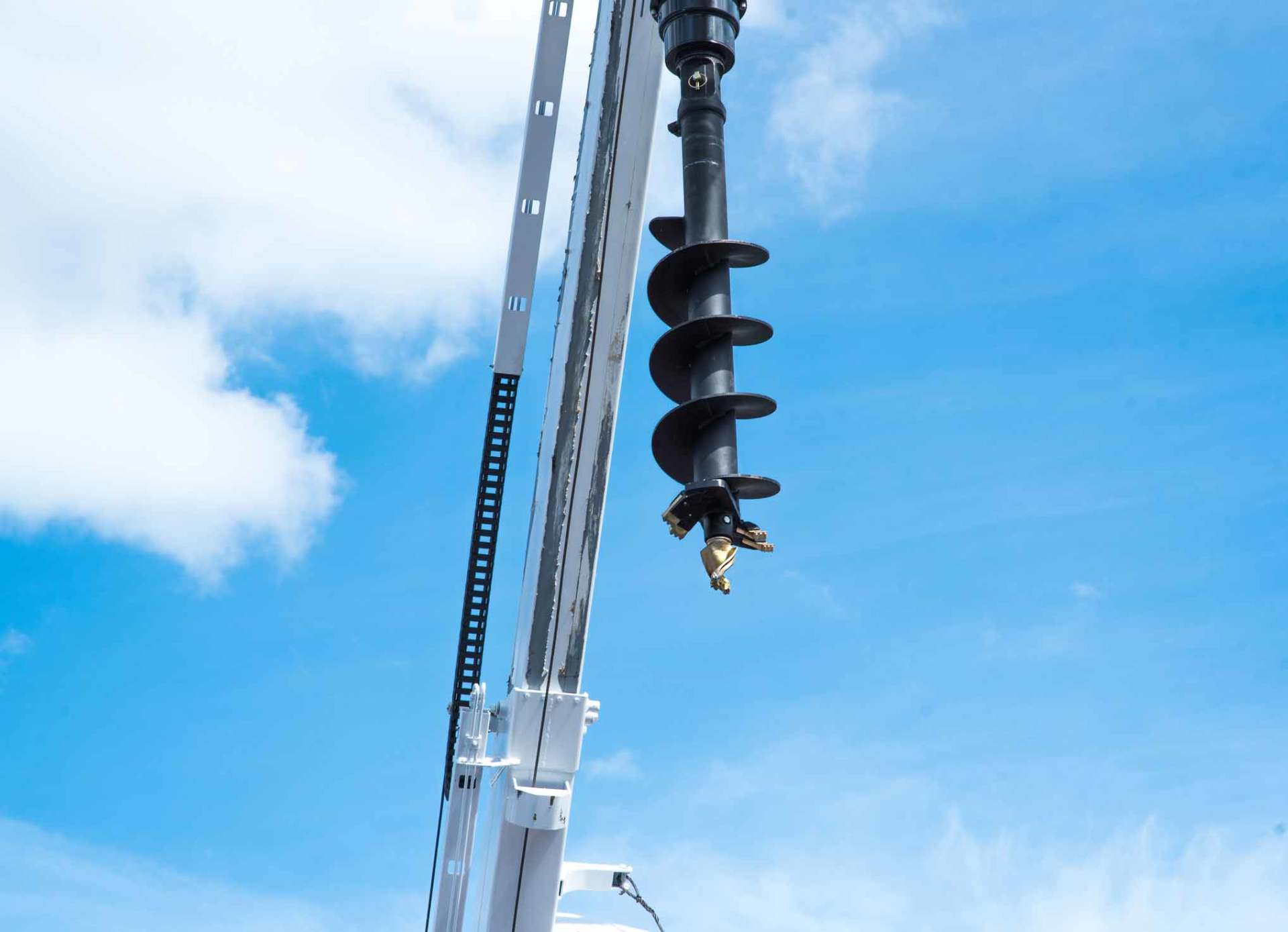
Directional drilling is one of the most widely used and versatile of all drilling techniques. Yet few people outside of the drilling industry possess an understanding of this highly effective technique. If you would like to improve your knowledge of contemporary drilling, then read on. This article will get you up to speed with some of the most important things to know regarding directional drilling.
Basics
Directional drilling, at its simplest, involves the creation of non-vertical wells. In other words, the shaft of the well does not penetrate straight down through the ground, On the contrary, it veers off to the side at an angle. In the most extreme type of directional drilling, known as horizontal drilling, the shaft ultimately assumes a position parallel to the ground above.
Advantages
Directional drilling offers a number of key advantages when it comes to harvesting the contents of a well, whether oil, gas, or water. For one, directional drilling means that the head of the well does not need to sit directly above the reservoir. This means that the contents of the well can be accessed even when buildings or other structures prevent vertical positioning.
This aspect of directional drilling also allows engineers to access reservoirs located underneath bodies of water. As a result, directional drilling has played a key role in offshore drilling operations. It permits engineers to gain access to key resources without the enormous expense of setting up off-shore drilling rigs.
The nature of directional drilling also means that multiple wells can be set up to harvest the contents of a given reservoir. This can greatly facilitate the extraction of resources.
Likewise, directional drilling allows a central wellhead to operate multiple bores. In other words, a single well can effectively harvest the contents of multiple reservoirs.
Process
A directional well resembles a vertical well until the kickoff point, which is where the well's shaft bends. Installing a directional well involves the use of a so-called drill string, which itself consists of multiple sections of drill pipe connected by drill collars. At the tip of the drill string lies the drill bit.
For the vertical portion of the well, workers operate the drill string in the same fashion as when creating a straight well. This involves rotating the entire drill string from the surface. Once the drill string has reached the kickoff point, however, this tactic will no longer prove effective. Instead, a mud motor must be used.
A mud motor allows the drill bit to rotate independently from the rest of the drill string. It does so thanks to the power provided by the positive displacement pump located inside of the motor. The mud motor remains attached to the drill string during vertical drilling. However, the mud motor will not come into play until the kickoff point has been reached.
Horizontal
As noted above, horizontal wells differ from other types of wells in that the shaft ultimately becomes parallel with the surface of the ground. Technically, any well with a wellbore with greater than an 80-degree angle can be considered a horizontal well. Besides increasing the reach of the well, a horizontal well also acts to boost production levels.
Rather than simply accessing the resource through a single point, a horizontal well crosses its entire width. This greatly increases the amount of resources it can gather in a given amount of time. In fact, a horizontal well may boost production levels up to 20 times greater than that of a vertical well.
For more information about wells and well construction, please don't hesitate to contact the experts at McCall Brothers Inc.